For most of us, the word “robot” conjures something like C-3PO — a humanoid creature programmed to interact with flesh-and-blood people in a more or less human way. But the roster of real-world robots is considerably more varied. The list includes Boston Dynamics’ dog-inspired robots, Dalek-like security bots, industrial arms on an assembly line and any number of flying insect-inspired robots. If a machine is designed to do a complicated task in an automated fashion, it’s a robot.
A robot, it turns out, doesn’t even need to have a fixed shape. That’s the vision of researchers who work in modular reconfigurable robotics and are pursuing bots that can assemble themselves, by rearranging similar or identical parts into whatever shape suits the task at hand. These robots can take the form of snakes, lattices, trusses and more, and can be set to any challenge — providing construction support, doing repair work or scouring for survivors after a natural disaster.
Or rather, they will hopefully do all that some day. In May 2019, the Annual Review of Control, Robotics, and Autonomous Systems surveyed both the promise of modular reconfigurable robots (MRR), and the many barriers that remain before they can become a reality. To get a sense of where these reconfigurable robots are right now, and where they could be in the future, Knowable Magazine spoke with University of Pennsylvania roboticist Mark Yim, one of the coauthors of the report and director of Penn’s General Robotics, Automation, Sensing, and Perception (GRASP) Laboratory.
This conversation has been edited for length and clarity.
What are modular reconfigurable robots?
LEGO is one analogy that people often use. LEGO bricks are modular and can be rearranged in lots of different ways, so that would be kind of like the modular reconfigurable robots, except these would be LEGO bricks that can rearrange themselves. Very often there will be one type of module, with hundreds of identical units; the reconfiguring of those modules is a big part of the research.
Another analogy comes from the very first modular robotics paper in 1988, when Toshio Fukuda and his colleagues in Japan had this idea called CEBOTS, or cellular robotic systems. The idea was that you have different cells in your body. Similarly, you could have robots that could come together and have a whole organism.
If you are not among that particular community, modular reconfigurable robots can be a little bit broader. In the Annual Reviews article, we talked about a typical standard milling machine where we have different types of tools that go into it. It’s modular in the sense that these tools can be swapped out, but they’re not identical. It’s a very different type of thing.
What would the goal of a modular reconfigurable robotic system be?
You’ve actually hit on one of the important, yet difficult issues with modular reconfigurable robots. One of the characteristics is that they reconfigure into different shapes. They can do lots and lots of different things. Usually that means that they don’t do most of them very well, at least not optimally. So the types of situations in which they work the best are those that require lots of different uses. The examples we’ve given in the past are things like planetary exploration. If you want to send something to Mars, you don’t know what you will find there, so a robot that can do lots of different things will be useful.
A near-term thing that most robotics researchers always talk about is search and rescue. You’ve got a building that’s fallen. You don’t know if you’ll need a wheeled robot or a legged robot. You don’t know if you need something small enough to go through tight spaces or under rubble, or big enough to move that rubble, or tall enough to look over a wall to see if something’s on the other side. You don’t know if you need to lift up objects. So having a system that can adapt, rearrange itself and change its functionality for the situation would be one in which modular reconfigurable robots would excel.
Can you describe some of the main types of modular robots?
Maybe the most popular type among the reconfigurable robotics research community is what we call the lattice configuration. This is a little bit more like LEGO bricks. The modules form a lattice as you put them together. The reason why they may be most popular is because they are a bit easier to program. It’s easier to think about how you get them to rearrange.
A video displaying the ModQuad, a group of drones that can self-assemble from individual units into a number of larger shapes. In some cases, the ModQuad fleet has been used to carry light objects.
CREDIT: MODULAR ROBOTICS LAB / UPENN
There was a Carnegie Mellon group that came up with an application they called “telepario.” If television is a visual medium, telepario was the idea of making a system that could make a physical shape that you could change. So instead of taking a video of a person and transmitting it somewhere, you could take a 3D capture of that person and use lattice-style robots to translate it into a remote 3D system that would move as the person moves. Of course, that’s really hard, and we’re not that close to making that system. Part of the reason it would just be used for 3D representation is because we don’t know how well that system could work in an environment. Could it move objects? Maybe not.
There’s another kind, which we call a chain-style reconfigurable robot. They form shapes more like standard robot arms and industrial arms. That one is better for doing typical robot tasks and assembly. The modules tend to need to be larger — usually you can’t have millions of modules; you have 10, 20 or 30.
What does it take to make something self-reconfigurable, rather than something that has to be reconfigured by hand?
The dividing line is not that crisp, actually. Having something reconfigure itself requires basically a docking mechanism that you can actuate, and you can get two parts to attach and detach automatically. There are a variety of things like that around now. Like refueling on jet fighters: They have this thing where a fighter jet flies up behind a tanker with a trailing refueling tube and docks with the end of the tube. That’s a very simple, one-element docking, and it’s definitely self-reconfiguring. But is it a modular reconfigurable robot? Not quite as we think of it. In our research, you need more than a handful of modules, all of which can attach, detach and rearrange themselves.
How do you make a good docking system?
That’s really tricky. With magnets, you can get strong attachments, but sometimes it’s hard to make them detach. There’s also glue, you can weld things or you can have screws — there’s lots of different ways to get things to attach, but getting them to detach is an interesting problem.
For example, the classic mechanical engineering style is to have hooks or latches that grab onto things and release. One of the issues that we’ve had with this is that those systems can be large: Over 50 percent of the volume of a particular module might be the latching and docking mechanism. So a good portion of that robot is not useful for the task that it’s doing, because it’s made for the reconfiguration part. So that’s another way in which things aren’t necessarily the most efficient. But those things can be very strong and release with zero force.
The SMORES-EP module is a versatile, autonomous modular robot able to take stock of its environment and then reconfigure its shape so it can navigate the space. The modules have wheels and lock together via electronically triggered magnets. Here the units assemble into at least three configurations — though even more are possible. The video has been sped up to 2x, 8x and 4x, respectively, for each configuration.
CREDIT: MODULAR ROBOTICS LAB / UPENN
There are people trying to come up with something like a switchable glue. Often what will happen is you have something that’s not terribly strong as a glue; it’s kind of like an adhesive. And then when it releases, it’s not completely releasing either. It’s still kind of tacky. The ratio of bonding strength to releasing forces is not great, but it takes very, very little space. Depending on the mechanism for actuating it, you could release the bond with electricity, heat or sometimes light.
One group also came up with melting a low-temperature alloy, which can be very strong and doesn’t take a huge amount of space. But detaching it means melting it and that does take a lot of energy. And there’s some question about how many times you can repeat that before it starts to fail. So you may run into robustness issues.
A lot of people dream about making tiny, tiny modules. Science fiction movies often come into play. People think about the Terminator movies with a liquid metal robot — molecule-sized modules turn into a Terminator. People are trying to make the module as small as possible, but reaching that small of a size is still far in the future.
What areas of technological development are helping to bring these modular robotic systems into a real-world setting?
The thing that I think is exciting is the truss reconfiguration systems.
Trusses are naturally modular. Making them reconfigurable basically gets past the constraint of having modular systems that are small, weak and require millions of moving parts, which just makes things very difficult from a practical point of view.
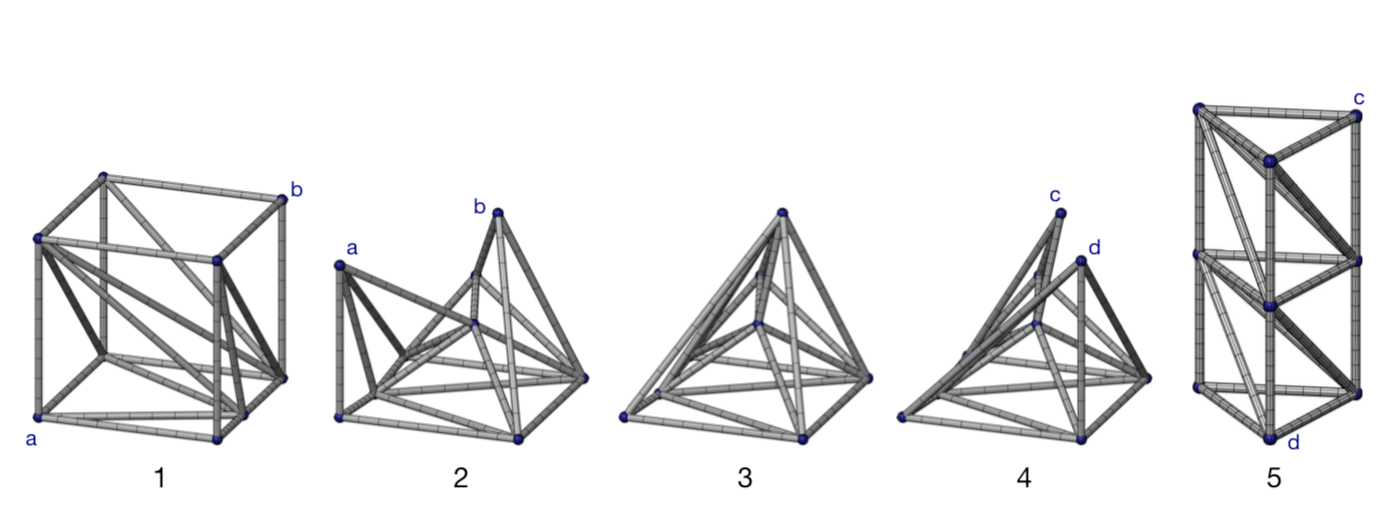
The Variable Topology Truss, pictured above, is a modular robotics system made of identical units that can assemble into various shapes. One use could be the formation of a support system in case of an emergency.
CREDIT: GRASP LAB / UPENN
The variable topology truss project we’ve been working on doesn’t have to be field-ready or so strong that it can shore up buildings. It can be at a human scale. The robots could move objects around that weigh tens of pounds instead of tons. Even 10 pounds can be a large load for most of these really small modular systems. So scaling things up to human size is making things more practical.
I think if we take a step back, there’s probably an intermediary approach where we can do things that are not quite so ambitious, but more practical and may be nearer term as well.
What is the first of these systems going to look like when it becomes a reality?
That’s a tricky question, partly because what it looks like, or what shape it is — that’s the variable. It’s a blob, so it can take whatever shape we want it to. I guess the bigger question is, what do we think it might do? We want to think visually, imagine that something is the size of a person or a dog or something like that.
But if it’s a bunch of trusses, the beams can change their length and rearrange their attachments. So it could be any shape you wanted.
What do you envision the farther future looks like?
The dream is that they become useful for the average consumer. One of my former colleagues came up with a concept he called “the bucket of stuff.” It’s just a bucket of modules and you say, “I need to make the bed.” The robot climbs out, makes the bed and goes back into the bucket. Or “Change the oil in the car — take whatever form you need to do that task” — a kind of generically useful robot system that doesn’t have to be humanoid shape, but can be anything, and therefore is more versatile. I think when you can get something to be low-cost and that useful, it takes a while, but that’s the dream.