What will it take to recycle millions of worn-out EV batteries?
In Nevada and other US states, entrepreneurs are anticipating the coming boom in retired lithium-ion batteries from electric cars and hoping to create a market for recycled minerals
Support sound science and smart stories
Help us make scientific knowledge accessible to all
Donate today
Thirty miles east of Reno, Nevada, past dusty hills patched with muted blue sage and the occasional injury-lawyer billboard, a large concrete structure rises prominently in the desert landscape. When fully constructed, it will be a pilot for a business that entrepreneurs envision as a major facet of America’s future green economy: lithium-ion battery recycling.
Construction manager Chuck Leber points out bays where trucks will drop off batteries, and deep drains in rooms to catch leaking chemicals. He shows me a two-foot concrete slab under the building — a hefty foundation so that workers can move equipment and adapt the plant while refining the recycling process. Later this year, the first batteries will pass through the facility; the goal is to ramp up to handle 20,000 metric tons of batteries a year.
The 60,000-square-foot plant owned by the American Battery Technology Company is an optimistic endeavor to address the inconvenient environmental downside of electric vehicles — their resource-demanding battery packs. It is also a test of whether business leaders can live up to their promises to help build a circular economy: one in which materials are reused indefinitely, minimizing the need to continually pry more minerals from the earth.
Since 2019, electric vehicles — EVs — have more than tripled their share of the auto market, and 6.6 million were sold globally in 2021. Facing pressure and sometimes outright regulation to reduce their climate footprint, many automakers have pledged to stop sales of new combustion-engine vehicles by 2040. “In five years, we are aiming for having tens of millions of electric vehicles on the roads,” says Alexandre Milovanoff of the sustainability consulting company Anthesis Group, who has studied how an EV transition would affect America’s electrical grid. “We’re talking about a market that is exploding.”
To feed the rising EV battery demand, the US government and companies are investing in domestic mining for the needed minerals — including nickel, manganese, cobalt and lithium (the price of which more than quadrupled in 2021). But they are also looking for ways to reduce dependence on newly mined materials through recycling. In March 2022, President Joe Biden invoked the Defense Production Act to bolster supplies of the in-demand minerals, directing domestic investments both in mining and in other forms of recovery.
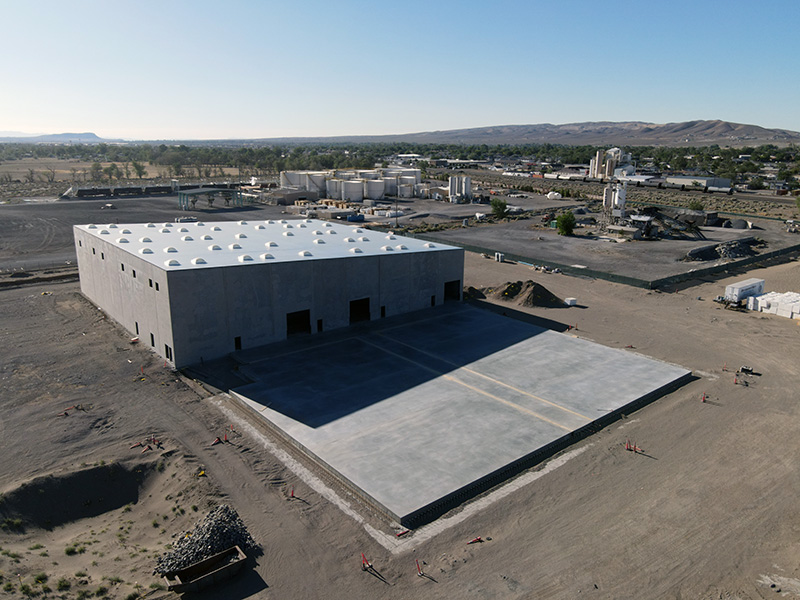
American Battery Technology Company is hoping to accelerate domestic battery recycling by building a 60,000-square-foot lithium-ion plant in Fernley, Nevada.
CREDIT: AMERICAN BATTERY TECHNOLOGY COMPANY
Researchers say that figuring out recycling could help to avoid the environmental risks of more mining and a buildup of hazardous battery waste — but reprocessing these batteries and refining the metals they contain for reuse is difficult and costly, and many remain skeptical of how truly circular that supply chain can ever be. “An electric vehicle battery is a very complex piece of technology with a lot of different components in it — so a recycling facility is going to be very complicated,” says Michael McKibben, a geologist at the University of California, Riverside. “In the long run, that’s going to be important, but in the short run, it’s got a ways to go.”
Sourcing specific minerals
To power a car, electrons in the battery move from the negative electrode, the anode, to the positive electrode, the cathode. Typically, the anode is made of copper and graphite, while the cathode consists of a class of compounds called lithium metal oxides — ones that contain lithium plus other metals such as cobalt, manganese and nickel.
All of these metals must be sourced — and recycling alone cannot yet meet market needs. Though the US has numerous copper mines (and obtains a sizable chunk of copper from scrap recycling), nearly all of the other metals in lithium-ion batteries come from mines in other countries. More than 80 percent of global lithium comes from Chile, Australia and China, while more than 60 percent of cobalt comes from the Democratic Republic of Congo.
This overseas reliance can come with costs. Much of the lithium mined today, for example, comes from the fragile Atacama Desert in Chile, where the metal is recovered by evaporating salty brine in massive ponds. It’s cost-effective, but researchers and local communities have raised concerns over toxic wastes and the depletion and contamination of water supplies; by one estimate, it takes 500,000 gallons of water — largely lost to evaporation — to concentrate a single metric ton of lithium. Sourcing battery metals also has been connected with human rights abuses in some locations, such as cobalt mining in the Democratic Republic of Congo, where companies have been accused of using child labor, paying workers poorly and failing to provide basic safety equipment.
Electric vehicles are powered by large battery packs composed of thousands of individual cells. Each cell contains four main components: a negative electrode or anode, a positive electrode or cathode, a plastic separator between the electrodes, and an electrolyte fluid that the lithium ions flow through. These components, particularly the cathode, require significant amounts of energy and materials to produce.
There’s also a greenhouse-gas price to pay for the long-distance transport of materials: Before anyone even gets in the driver’s seat of a brand-new electric vehicle, some EV battery materials have already traveled tens of thousands of miles. (Still, electric vehicles — with few exceptions — have a smaller carbon footprint than gas-powered cars, and electrifying transportation is key to slashing carbon emissions to stave off disastrous levels of climate change.)
For now, mining remains a need, and researchers think it’s possible to reduce its impacts through domestic operations and new technologies. But they say it is also crucial to ramp up the technology and business models for recycling. After thousands of charges and discharges, cells of lithium-ion batteries dry up and cracks form in the cathode materials, until the battery can neither hold nor deliver enough charge. Millions of EV batteries will soon be reaching this point, and if they’re deposited at the dump, they can leach toxic chemicals and even catch fire. A few US companies collect batteries for recycling, but this capacity lags behind the volume of spent lithium-ion batteries from cars, phones, computers and other electronics. In 2019, US recycling companies diverted from landfills about 15 percent of all retired lithium-ion batteries.
The challenges of recycling
Profitability is a major barrier. Though lithium-ion batteries contain valuable metals, they are challenging to take apart and the minerals are hard to extract from the tight layers of inorganic and organic compounds. By one estimate, the cost of recycled lithium is five times that of virgin lithium from brine-mining. Compare that with lead-acid batteries in combustion cars, which are almost entirely diverted from landfills and recycled. “It’s easy as pie to recycle a lead-acid battery in comparison to a lithium-ion battery,” says geologist Jens Gutzmer, director of the Helmholtz Institute Freiberg for Resource Technology in Germany and coauthor of an article about building a circular metals economy in the Annual Review of Materials Research.
The recipe for lithium-ion batteries requires minerals sourced around the world, sometimes in countries with relatively weak environmental and labor standards. The top sources for some major battery minerals are shown here.
Another problem is that today’s main lithium-ion battery recycling processes are also not particularly efficient. A process used by many recyclers, pyrometallurgy, involves melting down the batteries and burning off plastic separators to extract the coveted metals. Pyrometallurgy is energy-intensive, emits toxic gases and can’t recover some valuable minerals, including lithium, at all.
With growing EV sales, a massive wave of dead electric car batteries will soon exacerbate recycling problems. By 2028, researchers predict that the world will have more than a million metric tons of them to deal with. “I like to compare it to the plastic industry — we have a lot of plastic waste, and people are not really dealing with that — and I’m just worried that this will be happening also with batteries,” says Laura Lander, a materials scientist at King’s College London. And yet if it could be made profitable, scaling up EV battery recycling could, by 2040, reduce the global need for newly mined lithium by 25 percent, and for cobalt and nickel by 35 percent, according to one report prepared by the Institute for Sustainable Futures at the University of Technology Sydney in Australia.
Efforts to improve battery recycling are underway at the Department of Energy’s ReCell Center, a collaboration with national labs and universities launched in 2019. There, researchers are working to scale up what’s called “direct recycling.” This method aims to recapture the cathode material — a carefully manufactured powder — without melting or dissolving the whole battery and destroying the powder in the process. “They put a lot of time and effort into making these beautiful, spherical particles that are about 10 microns in diameter with the right crystal structure,” says Albert Lipson, a materials scientist at Argonne National Laboratory and the ReCell Center.
Lipson’s research team developed a chemical process to successfully recover cathode powder, which can then be rejuvenated by adding fresh lithium — returning the charging capacity that was lost as the original battery aged. The direct recycling method could make it more profitable to recover battery components while producing fewer greenhouse gas emissions than other recycling processes that use energy-intensive steps to re-manufacture cathode materials. (These involve, at one point, putting the material in a massive furnace.) ReCell’s direct recycling is being done only in laboratory-size batches right now, but Lipson says his team is working with companies to scale up the process.
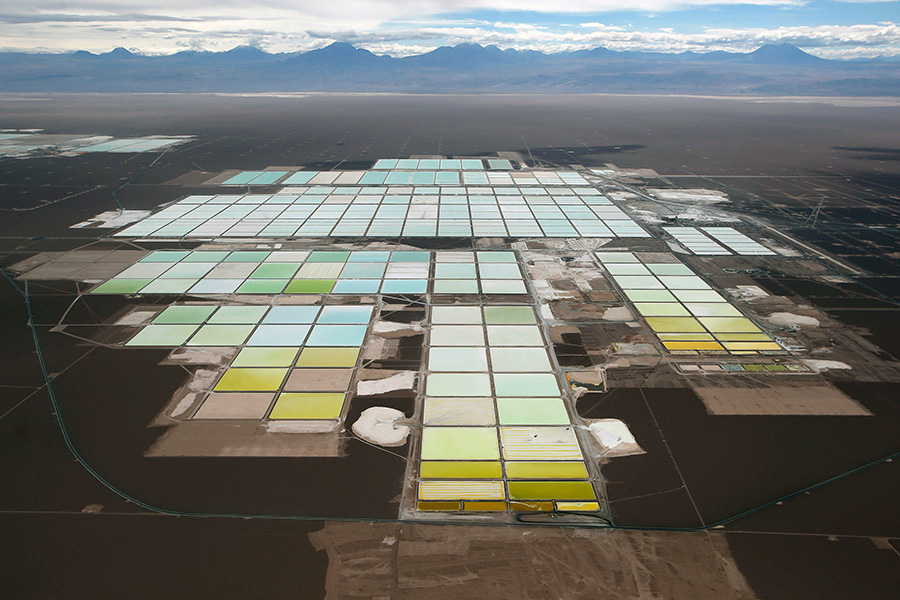
In Chile’s Atacama Desert, lithium-mining operations use massive evaporation ponds to concentrate and extract the metal. Beyond its large footprint of disturbance, the practice has led to concerns over depleted water supplies, and pollution.
CREDIT: REUTERS / ALAMY STOCK PHOTO
Battery recycling startups, for their part, are primarily using a technique called hydrometallurgy that dissolves the batteries in acid. Liquid solvents are then used to extract the minerals. Though hydrometallurgy isn’t new, the recycling companies — including American Battery Technology Company and Redwood Materials, both based in northern Nevada and headed by former Tesla engineers — say they are making the process more efficient and recovering more material than in the past.
Ryan Melsert, who heads American Battery Technology, says his time at Tesla’s Gigafactory — a gargantuan facility assembling batteries outside Sparks, Nevada — clued him in to ways to improve the recycling technology. Instead of shredding batteries as old-school hydrometallurgical recycling does, his company will use machines to break down used batteries, and then will separate and sell the lower-value components such as plastic, aluminum and steel. Proprietary chemical reactions will then extract nickel, cobalt, manganese and lithium.
“Instead of just dropping a battery in a furnace or a shredder,” Melsert says, “what our team has done is essentially take many of the same techniques we developed on the manufacturing side and we now operate them in reverse order.” He says the process can recover more than 90 percent of the high-value elements.
Getting the batteries from cars
But to recycle batteries, these startups will need to ensure that the packs make it to their facilities to begin with — a challenge in and of itself because facilities that process junked cars today don’t have protocols for EVs, including how to handle the batteries. Melsert says his company hopes to build on new partnerships with General Motors, Ford and Stellantis (which owns several brands including Dodge, Jeep and Maserati) to ensure that when a car is traded in, the battery will be sent for recycling. And Redwood Materials has announced collaborations with Volkswagen, Toyota, Ford and other automakers on battery collection and recycling.
As I walk with Leber, the construction manager, across American Battery Technology’s future recycling facility, he shows me where the finished goods warehouse will be located, across the building from the truck bays. During the first phase of operation, these finished goods will consist of “black mass,” a crumbly mixture of the valuable metals that will be sold to smelter companies for further refining and resale to battery manufacturers. Eventually, the company plans to add a second stage that will further refine this mix into separate minerals on-site.
To meet a carbon-emissions-cutting goal that would keep global temperature rise to well below 2 degrees Celsius (the Sustainable Development Scenario), the International Energy Agency projects that demand for several key minerals will skyrocket. Demand will also increase, albeit less sharply, if countries just act on their current commitments (Stated Policies).
American Battery Technology, along with Redwood Materials, Retriev Technologies and Canada-based Li-Cycle — the four main builders of EV battery recycling capacity in the US — have visions on their websites suggesting they are striving to build an infinitely recyclable supply chain. But is truly infinite reuse of battery minerals possible? Experts like Milovanoff and Gutzmer say that’s unlikely due to barriers like labor costs and energy needs. Still, it is technically possible to scale up and recycle more than 90 percent of the lithium, cobalt, nickel and copper in batteries, Lipson says — as long as the economics works out.
Ultimately, the success of battery recycling rests on whether it can be done cheaply enough. Even with improved technology, recyclers may face difficulties making their products cost-competitive with virgin minerals, says Aimee Boulanger, executive director of the Initiative for Responsible Mining Assurance, a coalition that works with companies to improve environmental and labor standards of mining projects. Incentives and regulations may also be needed: In the European Union, regulators have proposed guidelines for sustainable batteries that include their containing a proportion of recycled materials.
Melsert is optimistic. He thinks that since most battery minerals are mined internationally now, the transportation and import costs of virgin minerals will make domestically recycled materials competitive — a calculation supported by some research. In about another two years, he hopes to start building a facility that’s an order of magnitude larger to keep up with growing EV sales. And with demand for minerals outpacing what recycling will, for now, be able to provide, his company also has stakes in mining lithium in central Nevada.
“Some of the largest companies in the world are buying as much recycled battery metals as available,” he says. “The challenge, right now, is really about who can scale up the quickest.”
10.1146/knowable-092022-1
TAKE A DEEPER DIVE | Explore Related Scholarly Articles
