The greening of planes, trains and automobiles
We need new fuels to transport people and goods around the globe as society moves away from coal, natural gas and oil. Here’s how things are shaping up.
Support sound science and smart stories
Help us make scientific knowledge accessible to all
Donate today
As the world races to decarbonize everything from the electricity grid to industry, it faces particular problems with transportation — which alone is responsible for about a quarter of our planet’s energy-related greenhouse gas emissions. The fuels for transport need to be not just green, cheap and powerful, but also lightweight and safe enough to be carried around.
Fossil fuels — mainly gasoline and diesel — have been extraordinarily effective at powering a diverse range of mobile machines. Since the industrial revolution, humanity has perfected the art of dredging these up, refining them, distributing them and combusting them in engines, creating a vast and hard-to-budge industry. Now we have to step away from fossil fuels, and the world is finding no one-size-fits-all replacement.
Each type of transportation has its own peculiarities — which is one reason we have different formulations of hydrocarbons today, from gasoline to diesel, bunker fuel to jet fuel. Cars need a convenient, lightweight power source; container ships need enough oomph to last months; planes absolutely need to be reliable and to work at subzero temperatures. As the fossil fuels are phased out, the transport fuel landscape is “getting more diverse,” says Timothy Lipman, codirector of the Transportation Sustainability Research Center at the University of California, Berkeley.
Every energy solution has its pros and cons. Batteries are efficient but struggle with their weight. Hydrogen — the lightest element in the universe — packs a huge energy punch, but it’s expensive to make in a “green” way and, as a gas, it takes up a lot of space. Liquid fuels that carry hydrogen can be easier to transport or drop into an existing engine, but ammonia is toxic, biofuels are in short supply, and synthetic hydrocarbons are hard to produce.
The scale of this energy transition is massive, and the amount of renewable energy the world will require to make the needed electricity and alternative fuels is “a little bit mind-blowing,” says mechanical engineer Keith Wipke, manager of the fuel cell and hydrogen technologies program at the National Renewable Energy Laboratory in Colorado. Everything, from the electrical grid to buildings and industry, is also thirsty for renewable power: It’s estimated that overall, the global demand for electricity could more than double by 2050. Fortunately, analyses suggest that renewables are up to the task. “We need our foot on the accelerator pedal of renewables 100 percent, as fast as we can, and it will all get used,” says Wipke.
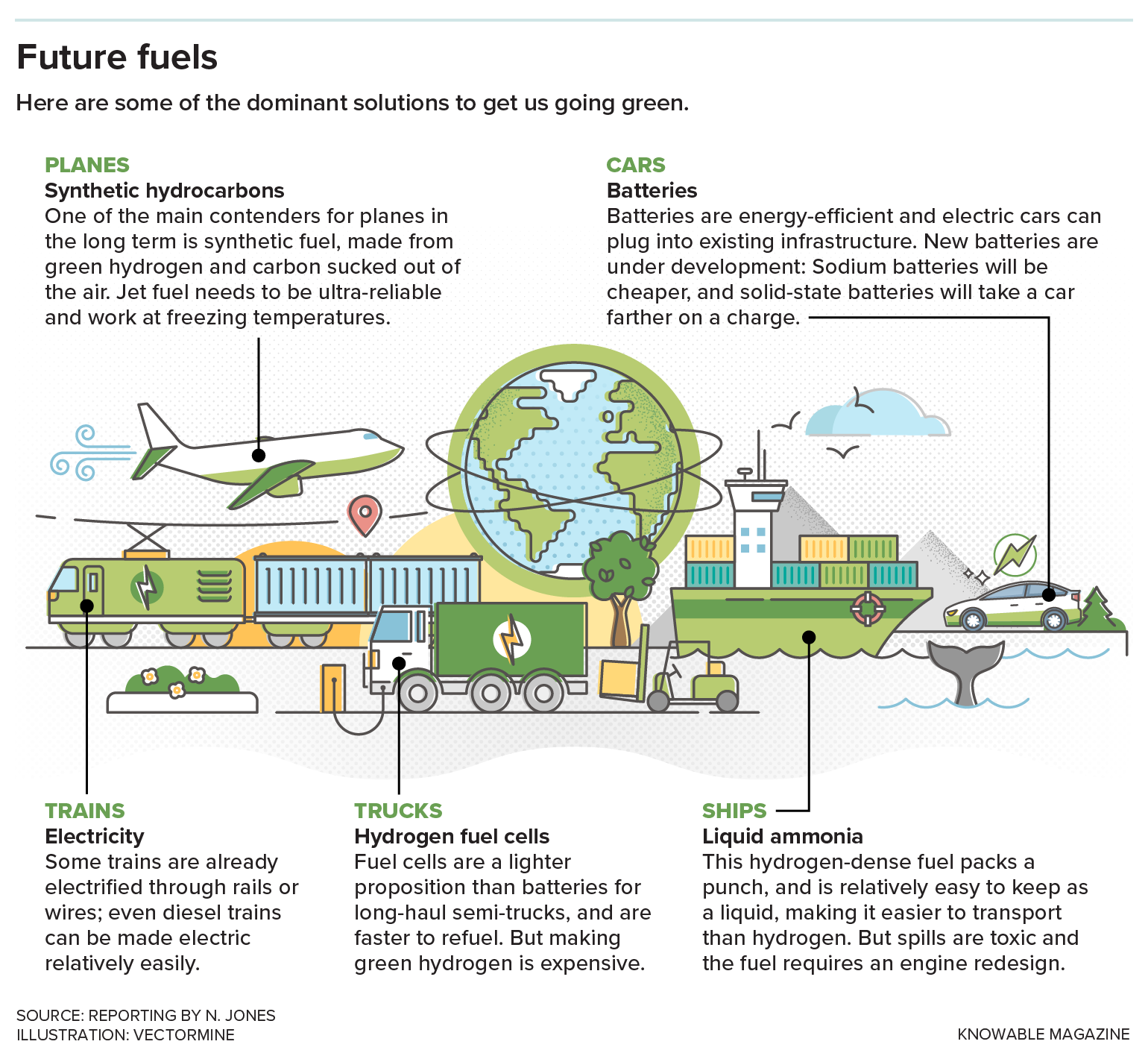
Each mode of transport has its specific fuel needs. Much is still to be settled, but here are some likely possibilities.
In order to stay below 1.5 degrees of planetary warming and limit some of the worst effects of climate change, the Intergovernmental Panel on Climate Change recommends that the world hit net-zero emissions by 2050 — meaning that whatever greenhouse gases we still put into the air we take out in other ways, such as through forests or carbon capture. Groups including the International Energy Agency (IEA) — a Paris-based intergovernmental organization that analyzes the global energy sector — have laid out pathways that can get the world to net zero.
The IEA’s pathway describes a massive, hard-to-enact shift across the entire world, including all kinds of transport. Their goal: to replace fossil fuels (which release long-captured carbon into the air, where it wreaks havoc on the climate) with something more sustainable, like green hydrogen or biofuels (which either don’t produce greenhouse gases at all or recycle the ones that are already in the air).
Although some transportation sectors are still in flux, we can now get a pretty good glimpse of what will likely be powering the ships, planes, trains and automobiles of tomorrow. Here’s a peek into that future.
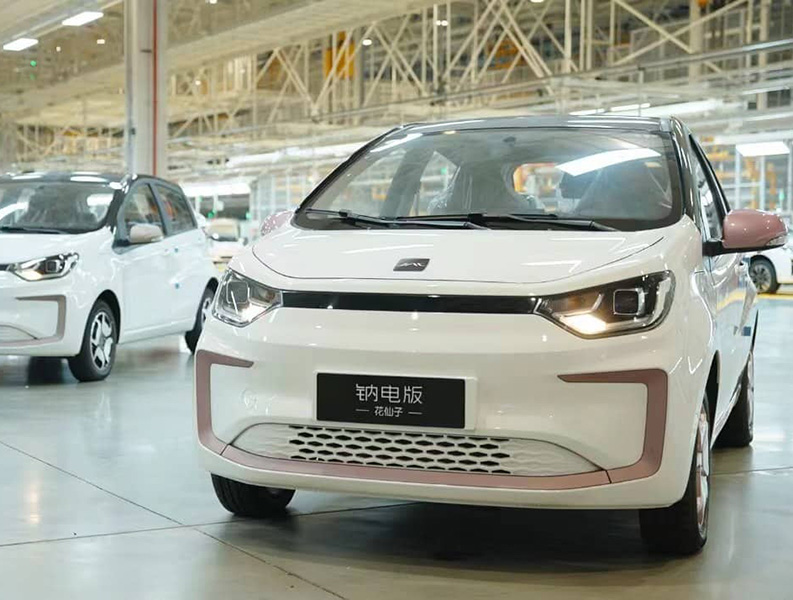
An electric car with a sodium-ion battery. Cars running on such batteries will be far cheaper than ones with lithium-ion batteries, but their range between charges will be far less.
CREDIT: JAC
Cars
Road passenger vehicles (including taxis, buses and motorcycles) together make up the biggest chunk of global transport emissions — about 45 percent of them.
Today, the clear winner for light duty traffic is electric batteries. (Of course, to cut emissions you need a green, renewable grid to provide the electricity; that transition is happening independently of transport.) More than a dozen nations have declared that all new cars must be electric by 2035 or earlier, and we’re on track to get there: About 14 million electric cars were sold in 2023, making up about 18 percent of new car sales. It wasn’t a clear path, though. “You learn more from your failures than you do your successes,” says Wipke: “There have been a lot of learnings along the way.”
Surprisingly, electric cars date back to the 1800s, when they were popular because they were simpler, quieter and less smelly to drive than gasoline versions. It was the invention of Henry Ford’s Model T in the early 1900s that made gas cars the winner; these were less than half the price of electric roadsters of the time and had broader reach. They were a hit: Today there are over a billion gasoline-fueled vehicles on the road.
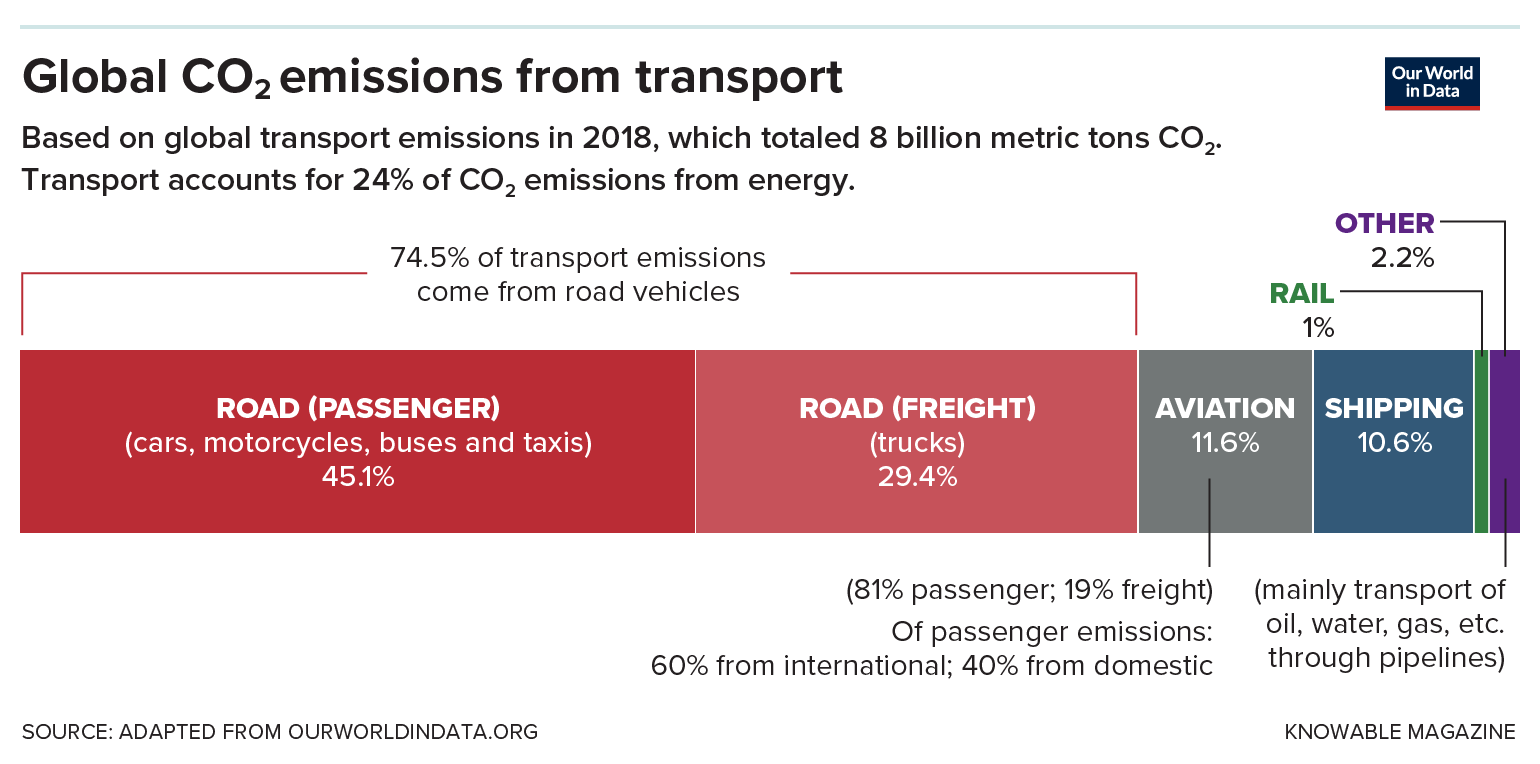
Moving goods and people around the world is responsible for a hefty portion of global carbon dioxide emissions. Here’s the breakdown for different modes of transport.
In the early 2000s, it looked like hydrogen fuel cells would be the solution to decarbonizing cars. These chemical cells are filled with hydrogen gas and then run like a battery — combining hydrogen with oxygen in the air to make power and water. Swapping to fuel cells would have given drivers a regimen similar to the one they were used to: the ability to go hundreds of miles between minutes-long refueling sessions. “The thought was, let’s not make people sacrifice or change their behaviors. Let’s give them something just like gasoline, but just a different fuel,” says Wipke.
But there were problems, predominantly in the logistical challenges of building a network of hydrogen filling stations, and the economics of producing all the needed hydrogen in a green way. “The big problem is not the vehicles — the vehicles are great. It’s the infrastructure,” says Lipman.
In the face of those issues, battery cars swung past fuel cells to market dominance, even though early versions of electric cars struggled to realize 100 miles in range and took hours, sometimes tens of hours, to fully recharge. The fact that you could just plug them in to existing electrical infrastructure was a huge bonus. And the overall efficiency of a battery is high — you don’t lose energy through the multiple steps of first creating a fuel and then powering your car. Plus, R&D promised ever better and cheaper batteries.
The challenge is achieving a high energy density (a lighter battery means a lighter car, which uses less energy per mile and so can go farther on a single charge), while keeping the battery cheap, safe, quick to charge, capable of powering bursts of acceleration, and operational across wide temperature ranges. Most electric cars today are powered by lithium-ion batteries, which have come a long way and are still improving. Since they were first commercialized in 1991, their average energy density by weight has more than doubled and prices have dropped by an order of magnitude. But there’s a limit to how good they can get, and lithium metal is prone to price spikes in the face of skyrocketing battery demand. So researchers and companies are pursuing two dramatic changes to battery tech.
As of 2023, some Chinese companies have started commercial production of sodium-ion batteries. Sodium is plentiful — it’s the sixth most common element on Earth — so it’s far, far cheaper than lithium, making it a great option for budget EVs. The trade-off is that sodium is heftier than lithium — each atom weighs 3.3 times more — which limits the energy that can be packed into any given battery weight. In other words, these batteries are heavy. Chinese cars with sodium batteries are expected to cost around $10,000 but go just 150 miles or so. Compare that to, say, a Tesla 3 (with a modern lithium-ion battery), which sells for more than four times as much but has over twice that range.
Car companies are also starting to promise solid-state batteries sometime within the next five years. Solid-state batteries get their name from the fact that they swap the liquid that’s typically in lithium-ion batteries with a thin layer of solid ceramic or polymer. This small-sounding shift offers safety benefits and opens the door to better options for the electrode ends of the battery. As a result, solid-state batteries promise much higher energy densities, though they haven’t yet hit the vehicle market. By 2027-28, Toyota plans to release a car with a solid-state battery that goes more than 600 miles on a single charge.
Overall, experts foresee roads filled with electric cars by 2050, but those cars will sport a variety of different types of batteries to suit users with different priorities: price or performance. We’re going to need a lot of batteries. In the IEA’s pathway to net-zero emissions by 2050, 60 percent of new car sales will be electric by 2030, requiring nearly 20 new gigascale battery factories to start up every year. That’s an epic — but doable — mission.
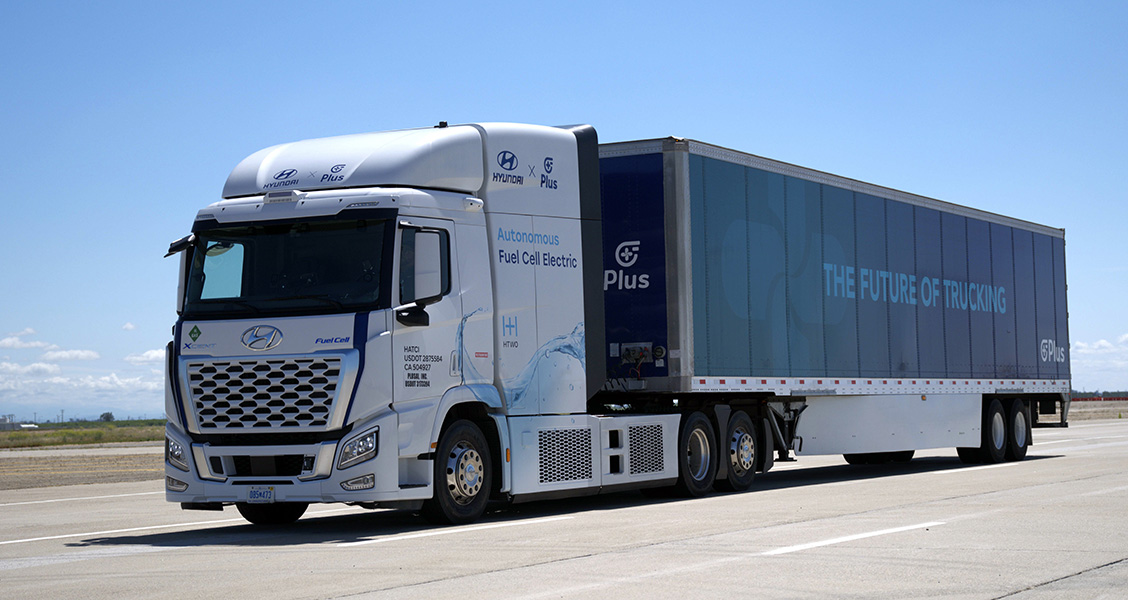
This electric truck runs on a fuel cell.
CREDIT: HYUNDAI
Trucks
Road freight vehicles — including massive semitrucks — make up the next-largest slice of the transport emissions pie, accounting for nearly 30 percent. For these heavy-duty road vehicles, especially long-haul ones, one preferred solution now harkens back to the original plan for decarbonizing cars: fuel cells.
Say you have an 18-wheeler pulling 80,000 pounds and need to go 500 to 600 miles. “To store that much energy in batteries could require up to 10,000 pounds of batteries on your truck,” says Wipke, “whereas maybe it’s 1,000 to 2,000 pounds of hydrogen storage, including the fuel cell.” And a hydrogen tank can be refilled in minutes. This translates to easier logistics for trucking companies, and less weight means less energy needed.
Like batteries, fuel cells have improved since their invention. “Hydrogen has made a lot of strides in the last 20 years, technically,” Wipke says. The pressure that the hydrogen can be stored under in a car has doubled, for example, so more fuel can be packed into a given space. And designers have overcome the problem of water freezing inside the fuel cell and breaking it.
Though the fiery inferno of the 1937 Hindenburg airship disaster gave hydrogen fuel an enduring bad reputation, experts point out that all fuels are flammable. Researchers typically say that a well-built hydrogen car is generally no riskier than a gasoline one — hydrogen, for example, is so light that it tends to float away quickly if a crash or leak occurs. There are also fail-safe technologies at hydrogen filling stations to prevent someone from just spraying it around, notes Wipke — which don’t exist for gasoline. But hydrogen filling stations are hard to make reliable. “You have compressors, you have flow valves. As a result, there’s more things that could break,” Wipke says.
Those kinks should be ironed out as fuel cell usage ramps up. In May, the Atlanta-based nonprofit Center for Transportation and the Environment opened the world’s largest-yet hydrogen fueling station. Located near Berkeley, California, it is designed to power 30 trucks that will take shipping containers and cars from the Port of Oakland to their next stop. Lipman is involved, with his team crunching all the numbers on the station’s reliability and usage, along with overseeing the trucks themselves. If all goes well, he says, it will expand. “We’re hoping to have thousands of trucks in 10 years.”
California isn’t alone in its pursuit of hydrogen. As of 2023, the US Department of Energy has invested $8 billion in a Regional Clean Hydrogen Hubs Program, establishing up to 10 centers that can make and distribute hydrogen fuel. Globally, hydrogen use in road transport increased by around 45 percent in 2022 over 2021 (although that’s still just tens of thousands of trucks and buses in total around the world).
A big challenge, though, is to make all the needed hydrogen in a green way. Although hydrogen is plentiful (it’s the most abundant element in the universe) and there are some natural geological deposits to mine, creating a pure, concentrated supply takes energy. The cheapest way to get hydrogen is to steam-reform fossil fuels, but this produces carbon dioxide. The cleanest way is to use renewable electricity to crack water into hydrogen and oxygen but making such “green hydrogen” is much, much more expensive.
As of 2022, hydrogen demand hit nearly 100 million metric tons, but less than 1 percent of this was made in a low-emissions way. According to the IEA’s net-zero pathway, the world will need twice this amount of hydrogen for fuels by 2030, including 11 million metric tons of straight hydrogen power for transport. The IEA has documented a lot of political support for green hydrogen, and a steep increase in the rate at which low-emission hydrogen production projects are being announced, which is all good news. But actual, real-world deployment, the agency notes, is “not taking off” and a lot more policy support is needed to get it to ramp up.
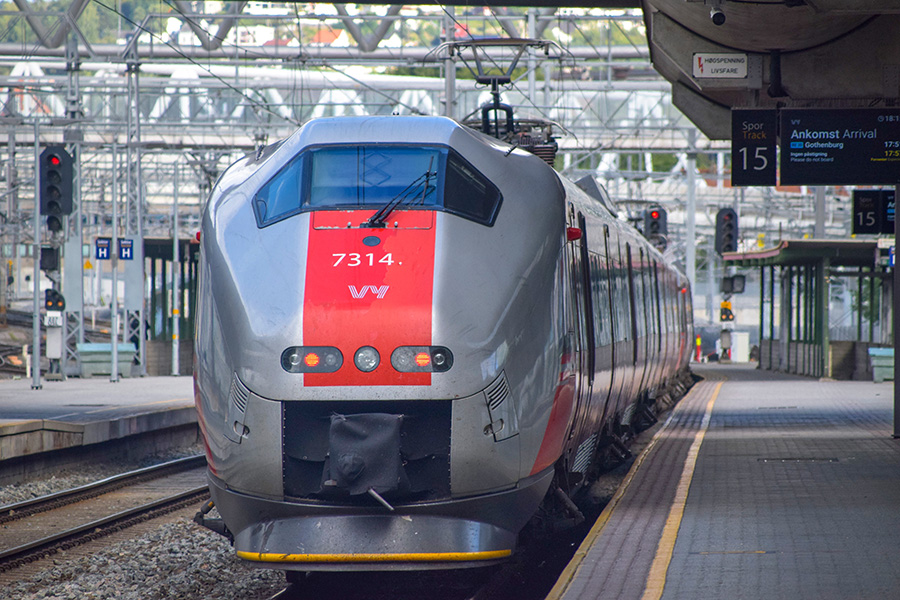
Many trains are already electrified, powered by electric rails or overhead wires.
CREDIT: NGCHIYUI / SHUTTERSTOCK
Trains
Rail is already the most electrified transport subsector, according to the IEA, and makes up only a slim 1 percent of transport emissions. So this is the smallest, most-solved problem of the batch.
Trains, like trucks, are heavy beasts that need a lot of power. But many trains already run on electric wires or rails. Others use a fuel, usually diesel, but turn that into electricity on board in order to power an electric motor (which has better torque than a fossil-fuel-fed engine). It’s a relatively simple step to swap out that diesel for something else, like hydrogen or batteries, to supply power for an already-existing electric motor. “Trains are pretty easy to electrify,” says chemical engineer Hartej Singh, who analyzes decarbonization for the nonprofit Rocky Mountain Institute in Washington, DC.
Expanding electric rail, the IEA says, is a good idea — especially if it replaces flights. Today, every mile a passenger travels on a train has, on average, one-fifth the emissions of the same distance traveled on a plane. But, the IEA notes, putting in a new electric rail line is an expensive proposition.
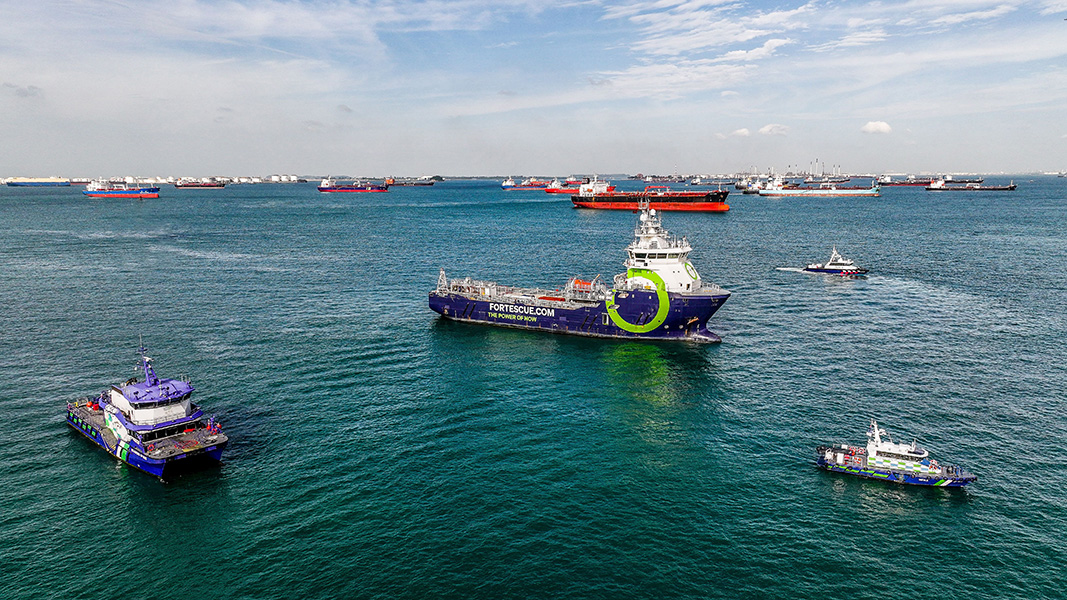
A ship powered by a mix of ammonia and diesel, shown here in the port of Singapore.
CREDIT: FORTESCUE METALS GROUP LTD
Ships
Shipping — accounting for about 10 percent of transport emissions — has a particular need to go extraordinary distances and lengths of time before refueling: Crossing an ocean calls for weeks-long journeys of thousands of miles.
Shipping currently predominantly uses bunker fuel — a high-sulfur variant of fossil fuel often described as the gunk left over at the bottom of an oil barrel. But that’s changing fast, thanks to International Maritime Organization goals, adopted in 2023, to hit net-zero emissions by close to 2050. “That’s basically the entire global fleet needing to transition off fossil fuels,” says Tristan Smith, an engineer at University College London who studies shipping. For now, just 1.2 percent of the ships in the global fleet use lower-emission fuels, but 21 percent of the new ships on order are designed to run on these alternatives. Smith sees a clear path ahead to get where shipping needs to go.
For now, one popular low-emission alternative is bio-methanol (made from plants). But this is a short-term distraction, says Smith: There’s simply not enough land to grow enough biofuel stock for the global fleet. For the long term, he’s betting on ammonia — NH3 — as the best solution.
This is a hydrogen-rich liquid fuel that provides a lot of oomph. Plus, we already know how to make it and move it around; globally some 150 million metric tons are produced every year, mainly for fertilizer. Ammonia counterintuitively works out to be cheaper than straight hydrogen, notes Smith (even though it has hydrogen as an ingredient), because pure hydrogen comes with the extra energy and cost burden of putting it under pressure and keeping it cold to store it. Ammonia, by contrast, is relatively easy to keep liquid. And though ammonia requires more storage space than fossil fuels, this matters less for ships than for, say, cars.
You do have to redesign your engine to run on ammonia, though. Ammonia is hard to ignite, and the engine needs catalysts to remove other pollutants, like the greenhouse gas nitrous oxide. All of this is being tackled: The Green Pioneer, run by Australian mining and green energy company Fortescue, is the first ship to trial an ammonia-burning engine (with some diesel in the mix), along with refueling strategies and safety protocols. The main problem with ammonia, says Smith, is that it’s toxic, so spills are nasty. All in all, Smith sees a clear path ahead for ammonia. “We can see a situation where there’s an explosion of ordering [of ammonia-engine ships] from the middle of next year,” he says.
Ammonia will put yet more strain on the demand for green hydrogen. By 2030, the IEA calls for an additional 8 million metric tons of hydrogen for ammonia-based transport fuels, on top of the 11 million metric tons of straight hydrogen for transport uses. There’s billions of dollars of investment already being plowed into green ammonia, Smith says. “We need lots of billions.”
There are additional ways to reduce emissions from ships — including shipping less cargo to begin with, improving logistics to run fewer ships shorter distances, designing sleeker hulls, and even putting up modern sails. That includes strange rotating poles called Flettner rotors that can help to propel a ship in a way similar to how a spinning baseball moves sideways in the air. All of them could help to whittle down shipping’s carbon burden.
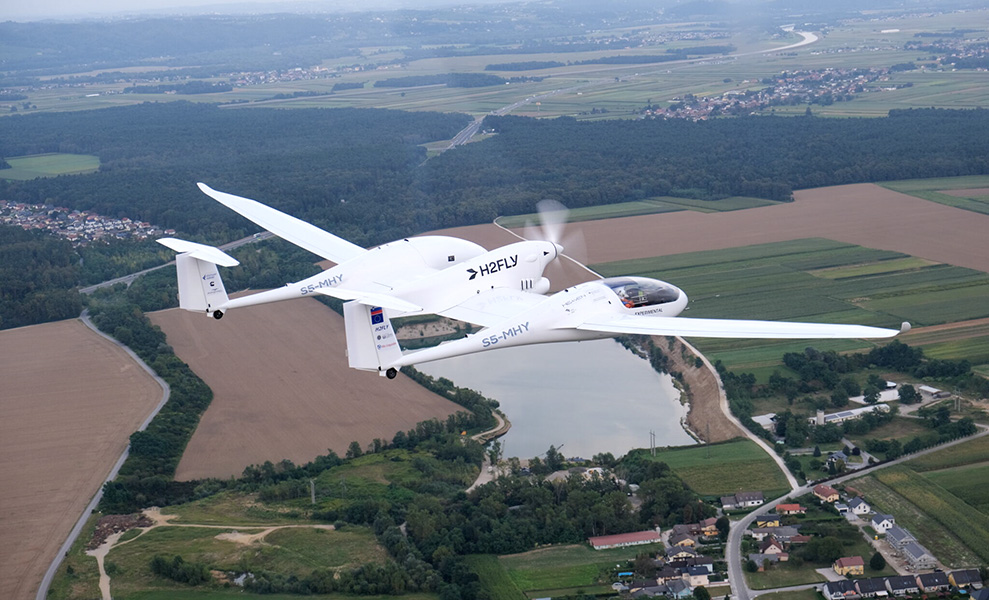
H2FLY’s electric plane is powered by liquid hydrogen. It took to the air in the world’s first piloted test fight in 2023, in Slovenia.
CREDIT: H2FLY
Planes
Perhaps the hardest sector to decarbonize is aviation, which makes up about 12 percent of the transport emission pie. A plane must fight gravity, so it can’t carry a fuel that’s too heavy. The fuel can’t take up too much room, needs to work at the freezing temperatures found at altitude, and above all, it must be reliable. “It’s one thing if a truck or a car loses its propulsion and it coasts to the side of the road. It’s much different if you’re in the air and you lose power,” says Wipke.
In 2022, the United Nations’ International Civil Aviation Organization pledged for the industry to become carbon neutral by 2050, so the race is on to swap out the current fuel, kerosene, for something cleaner: sustainable aviation fuels. Most of these fuels still spew carbon dioxide out of the tailpipe, but since many are made from something, such as plants, that originally removed carbon dioxide from the air, the net effect can be to cut emissions at least in half, if not almost entirely. As of 2022, around 300 million to 450 million liters of “sustainable fuels” were being used in aviation — but that’s less than 0.15 percent of the total market.
For now, the most cost-effective option for sustainable fuel is biofuel made from fats, oils and greases (such as used cooking oil) that have been chemically converted into kerosene. This is a mature, already-commercial technology, says the RMI’s Singh, who focuses on aviation fuels. But long-term, there simply isn’t enough of this source material. “We could probably only cover about 6 percent of demand by 2050,” says Singh.
The next option is biofuel made from forestry residue, such as fallen branches and logs or even nut husks. This source material could provide about as much fuel as waste oils, but the chemical conversion is more complicated; the one company Singh knew of trying to make this work commercially recently shut down its biggest plant.
One long-term option for sustainable jet fuel is to make hydrocarbons from recycled air. These synthetic fuels (sometimes called power-to-liquid fuels, or e-fuels) take carbon dioxide from the air and combine that carbon with low-emission hydrogen (yes, yet more low-emission hydrogen). Direct air capture plants, as they’re called, are industrial facilities that use liquids or solids like a sponge to sop up CO2 from the ambient air. These are just now ramping up to large-scale commercial operation: The planet’s first megaton-scale plant — sucking around half a million metric tons of CO2 from the air each year — should be opening in Texas in 2025.
Using straight hydrogen is also a possible long-term option, either by burning it in an engine (the way NASA launches rockets) or using it to run a fuel cell. But that requires special tanks to store hydrogen at high enough pressures and low enough temperatures to fit into a plane. “You need to reconfigure the entire way we think about airplane design,” says Singh. A few companies are taking the possibility of hydrogen flight very seriously, including H2FLY, a subsidiary of Joby Aviation, which ran a test flight of a small demonstration hydrogen plane in September 2023. Airbus and a partner are now working toward building a liquid hydrogen airport-refueling facility in Toulouse, France.
“I think we underestimate this skill of the engineers,” says Smith, who sees the difficulties with ammonia-powered ship engines and hydrogen-fuel-cell-powered planes as surmountable obstacles. “You just put some good engineers on a project, and they systematically work through everything.”
Batteries are also a possibility, especially for shorter, smaller flights like those taken by electric vertical takeoff and landing craft (eVTOLs), which are essentially flying taxis. A lot of long-shot research is being done now on batteries that are hard to make work but would have spectacular potential. Lithium-air batteries, for example would pull oxygen from the air on the go as one vital electrode ingredient, making them incredibly lightweight and well suited to aviation.
“We need to think of this as a jigsaw puzzle,” says Singh, with different pieces filling in different parts of the problem. Batteries might end up powering short hops, while fuel cells tackle regional traffic, and sustainable fuels get saved up for the long-haul flights that are too hard to electrify.
In fact, the whole transport sector is a puzzle, with many pieces needed to complete a picture that’s not quite clear yet. “I can’t see the future any better than anybody, or I probably would be retired right now,” says Wipke. “But I do really enjoy watching things evolve. The pace of development is tremendous.”
10.1146/knowable-070324-2
TAKE A DEEPER DIVE | Explore Related Scholarly Articles